When is pCBN Tooling an Appropriate Choice?
Let’s Take a Look at The Options.
When it comes to machining hard materials, traditional tooling materials such as carbide can quickly wear out and fail to provide the necessary precision and accuracy. This is where polycrystalline cubic boron nitride (pCBN) tools comes into play. pCBN is an extremely hard material that is ideal for machining hard metals, ceramics, and other difficult-to-machine materials. In this blog, we’ll explore when PCBN tools are appropriate for a manufacturing process.
First, let’s briefly cover what PCBN tools are. PCBN is a composite material made by sintering cubic boron nitride particles together with a metallic binder. This results in a material that is extremely hard and wear-resistant, making it ideal for machining applications that involve hard materials. pCBN tooling is made by bonding pCBN inserts onto a carbide substrate, which is then mounted into a cutting tool holder.
Now, let’s look at the situations where PCBN tooling is appropriate: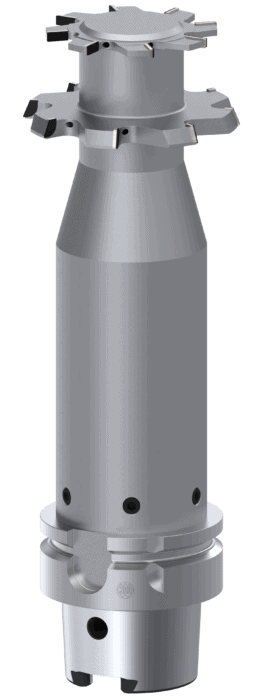
- Machining Hardened Steel – pCBN tools are ideal for machining hardened steel, which is a notoriously difficult material to machine using traditional tooling. This is because pCBN is harder than carbide and can withstand the high temperatures and pressures that are involved in the machining of hardened steel. pCBN tools can provide superior surface finishes and higher speed and feed cuts than other carbide tooling when machining hardened steel.
- Machining Other Hard Materials – In addition to hardened steel, pCBN tooling is appropriate for machining other hard materials such as cast iron, super alloys, and ceramics. These materials can also be difficult to machine using traditional carbide tooling, but pCBN can provide the necessary precision and accuracy to achieve the desired results.
- High Production Runs – pCBN tools are appropriate for high production runs where tool life and consistency are critical. Because pCBN is extremely wear-resistant, it can last much longer than carbide or other tooling materials, resulting in fewer tool changes and increased productivity. Additionally, the consistent and precise results provided by pCBN tools can help to reduce scrap and rework, further increasing productivity and reducing costs.
- Precision Applications – pCBN tools are appropriate for precision applications where tight tolerances and surface finishes are required. pCBN can provide superior surface finishes and dimensional accuracy compared to traditional tooling materials, resulting in parts that meet the required specifications.
In conclusion, pCBN tooling is appropriate for a variety of manufacturing applications where traditional tooling materials are unable to provide the necessary accuracy and tool life. From machining hardened steel and other hard materials to high production runs and precision applications, pCBN tools can help to improve the quality and efficiency of the machining process. While pCBN tools can be more expensive than traditional tooling materials, the benefits provided by pCBN make it a smart investment in many situations.